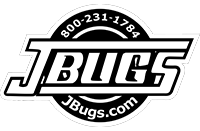
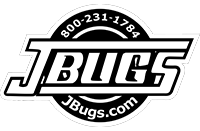
Your cart is currently empty.
Hi, Sam here with
JBugs.com. In our last video, we finished the assembly of a short block for our
1800cc stroker engine build for our 1971 Euro Look Super Beetle. With our
engine taking shape, well get started on the top end by test fitting our
pistons and cylinders setting the deck height and most importantly setting the
compression ratio for our engine. This step is often overlooked but crucial to
the power and performance of an engine. Higher compression produces more
output, but the byproduct of that is heat. On the other hand, if the
compression is too low the engine won't be efficient and actually ends up
wasting fuel.
Typically in VW engines
somewhere between 7 and 8.5 to 1 is the norm. We're going to set our engine at
about 8.25 to 1 towards the performance side of the spectrum. The top end
assembly begins by coating the ends of threads of our head studs with aviation
sealant and threading them into the engine case.
Our 1971 engine has a
deep stud at the number three cylinder. The top back threads at the number
three and the eight lower threads all use the longest studs. The top inner
studs are the shortest and the other three remaining top outer studs are the
middle length. The studs are threaded in by hand whenever possible a pair of
vice grips can be used gently otherwise.
Next, we'll get our
thick walled 88mm pistons and cylinders pulled apart and cleaned for test
fitting. The cylinders are somewhat unique. At the top, they are extremely
thick and require the use of heads board out for 90.5 cylinders. At the case
though, they're very thin. Since most of the load, pressure, and heat are at
the head not at the case, the pistons are actually a good alternative for those
who are looking for more displacement and performance out of a stock 1600cc
block.
The pistons are pushed
out of the cylinders, the rings are all pulled off, and the pistons and
cylinders are cleaned. At the engine stand, we rotate the engine so that the
number 3/4 side is at the top and lube up and test fit a wrist pin into the
number three connecting rod. It's removed, then a piston is placed over the
connecting rod and a lubed cylinder is slid onto the head studs, over the
piston and down into place on the engine.
With the crankshaft
rotated to top dead center for cylinder three, we can see that the piston
sticks out past the edge of the cylinder because of our longer stroke
crankshaft. Cylinder shims will be used to space the cylinder away from the
case. We rotate the crank to make sure the piston clears the crank and the
crank stops. We pull the cylinder up and see that the crankshaft is hitting the
skirt of the piston. This isn't out of the ordinary when using a stroker
crankshaft, and there are a couple ways of clearancing the piston.
We pull off the
cylinder, the wrist pin, and the piston. One way of clearancing would be to
notch the skirt to allow the piston to clear the crankshaft. The other way,
which we go with, is to cut the skirt clear. We measure the distance from the
edge of the crankshaft bottom dead center point to the bottom of the hole of
the connecting rod and note the measurement. We measure that distance from the
bottom center-line of the wrist pin hole in our piston and mark the skirts to
be cut there.
What you do to one side
of the piston ideally you'd do to the other to keep the piston balanced. What
you do to one piston, do to the remaining pistons to keep the engine and
rotating assembly as balanced as possible. The skirts on both sides of the
pistons are cut as close to equally as possible noting the measurement. A
sanding pad and scour pad, on an air powered angle grinder, are used to even
and smooth out the skirts and any rough edges on the piston.
The pistons are cleaned
up and we reinstall a piston to the connecting rod to check that the engine
rotates without hitting the crank. With the pistons now clear of the crank, we
can get on with setting our compression ratio and deck height. At our
workbench, we have an EMPI GTV2 cylinder head that is machined for 90.5 or in
our case thick walled 88mm cylinders. The head has %20 larger intake and
exhaust ports than stock heads
so it will flow better
and make more power than a stock head.
We chose a head with
40x35.5 stainless steel valves and dual valve springs. EMPI lists the cc's of
the compression chamber at 58, which we want to confirm, and at the same time,
we'll show you how to cc your heads using a head cc measuring kit. We thread a
12mm long reach spark plug into the head which is sitting level at our bench. Then
we apply a ring of assembly lube around the outer edge of the appropriately
sized disc, three discs are included to fit 85.5, 90.5 and 94mm heads, to
provide a seal between the disc and the head.
Next, we fill up a large
syringe with water, up to the 60cc line. We fill up the combustion chamber with
water until there's no air remaining. We know there is 2cc's left in the syringe,
60-2 gives us 58cc's, confirming EMPI's measurement. Now we use those known
measurements in our online engine calculator at JBugs.com. We enter the
following factors. Our bore is 88mm. The stroke is 74mm. The deck height will
be our variable so we leave it blank. Our cylinder head volume is 58 cubic
centimeters. We enter the compression ratio we want, 8.25. Clicking the deck
height button below tells us that a deck height of 0.026 inches will give us
the compression ratio we're looking for.
Now knowing the deck
height we want, at the engine, we set our number three cylinder to top dead
center. We do all our measurements and set the compression at number three as
it runs hotter than the other cylinders. So we make sure that if nothing else,
it is at our compression limit. The other three cylinders should be nearly
identical to number three but there's no harm in verifying the rest of the
cylinders if you'd like to be certain.
A deck height measuring
tool is set on top of the piston which is sticking out past the end of the
cylinder. With a set of feeler gauges on the outer edge, we measure the gap
between the top of the piston and the cylinder at 0.050 of an inch. We set two
0.040 shims on top of the cylinder and reinstall the deck height tool. A feeler
gauge is used on the inside edge of the tool and we get 0.030 of clearance
which is closest to what we're looking for.
As cylinder shims are
only made in multiples of 0.010. We'll use a copper shim between the cylinder
and the head which will compress a little bit and most likely get us very close
to the 0.026 thick heights that we want. In prepping for our next step and
knowing that our 0.080 shims will be used we mock up the number three and four
cylinders and pistons on our engine and install each of the cylinders with two
0.040 steel shims between the case and each cylinder.
We set our cylinder head
in place and install washers and nuts at the inner four studs
and snug down the nuts
in preparation for our next step. We've thrown around a bunch of numbers today
while setting our compression ratio and next we'll be setting up the rocker
geometry for our 1.4:1 ratio rockers. That is going to involve much more number
crunching, so we'll pause for now. Stay tuned for our next video. In the
meantime check out our other how-to videos and when it's time to order parts
for your vintage VW, stop by JBugs.com
Copyright © JBugs.
All rights reserved. All images protected by US and International copyright laws. No part of this website may be reproduced, distributed, or transmitted in any form or by any means.
All Prices subject to change without notice or obligation. Not responsible for typographical or photo errors. "Volkswagen", "VW","Beetle", "Super Beetle", "Bus", "Ghia", "Type 2", "Type 3", "Thing", "Rabbit", "Cabriolet", "Jetta", and "Golf" are trademarked by Volkswagen of America and are used for descriptive purposes only.