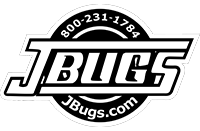
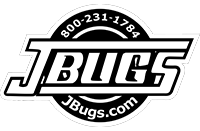
Your cart is currently empty.
Hello there, I'm Sam
with JBugs.com In our last few videos, we pulled apart the engine from our 1971
Super Beetle, as it wouldn't turn over. We discovered a dropped valve, a hole
in a piston and excessive crank end-play which meant the engine needed to be
fully rebuilt.
We were hoping that the
bottom end was in better shape as we were planning on a set of thick-walled
88mm pistons and cylinders, along with big valve heads and installing some high
ratio rockers. This would have increased the factory displacement from 1600cc, which
is actually 1585cc, by 94cc to 1679cc. More importantly, none of this would
have required splitting the engine case.
That opportunity is
gone, and while we'll still be using the same bolt on top end parts we
originally intended, we're going to build an 1800cc engine by adding a 74mm
crank to the mix. The intent of this rebuild will be to keep special machine
work to a minimum. While we did have to head to a machine shop to have the case
line bored, like anyone who is rebuilding an engine would have to, that was it.
Everything else for the rebuild can be done with common tools most of you would
have at home in your garage and a few inexpensive specialized tools here and
there.
This isn't a
high-performance race build though, and all the steps of our engine build can
be done by the average person. We aren't weighing every part, spin balancing
every component, or blueprinting the case. This will be a simple garage build. We
start by cleaning the crankshaft and so we don't have to mention it over and
over again, every part that we will be working with is cleaned completely with
parts cleaner and blown off before it's test fit or assembled.
Our engine case is clean
and all the passages have been flushed and blown out. Often times, the same
part is cleaned three or four times in between test fitting and final assembly.
We start at the bench with our crankshaft, which has been eight dowelled with
an offset pin, and we're matching it up to a lightened eight dowelled flywheel.
The crank is set up
right onto it to make assembling the rest of the components easier. We start
with the number three bearing and coat it and the crank with assembly lube and
slide the bearing onto the crank journal. Make sure the dowel pin hole is
offset towards the flywheel so the bearing will align properly in the engine
case later. The timing gear keyway is set in place on the crank.
Then we'll prep for
installing the cam and distributor drive gears which will not fit onto the
crank unless they are heated up or pressed on. As we don't have a press here,
and most of you don't have one at home either, we'll move outside, for safety, and
fire up a propane grill. The cam drive gear and distributor drive gear are set
in a pot of vegetable oil and placed on the grill. It takes some time but
eventually the oil and most importantly the gears get hot enough. More or less
once the oil itself starts smoking steadily, we're ready to install the gears. The
timing gear is pulled from the oil, with a set of tongs, grabbed with a welding
glove-covered hand, and set onto the crankshaft. Making sure the timing marks
are pointing towards the crank pulley side.
The gear slides down
freely and actually knocks the keyway loose. Some quick hands are needed along
with a punch and hammer which are used to straighten the keyway and then tapped
the gear down completely. Next, the full circle gear spacer is installed on top
of the timing gear and it's followed by the heated up distributor drive gear. The
grill is turned off and we'll move back inside to continue our build.
B the timing gear snap
ring is slid into place, with a pair of snap ring pliers, and tapped into
place, into the groove on the crankshaft. Next, are the rods. Seeing as how
stock rods won't last longer than 5,000RPM and our new engine build will easily
turn past that mark, we'll install a set of stock length chromoly
"eye" beam connecting rods.
New standard rod
bearings are installed and not that our connecting rods don't have a raised nub
like our stock rods to indicate the top. We instead look at the stamped numbers
on the rod ends [which sit along the top sides] and the bearing tangs, which
will sit at the bottom. The bearing and the rod journals on the crank are
covered with assembly lube.
The rods are set in
place making sure the rods and most importantly the rod numbers are aligned and
facing up. In our case, seeing as how we're using a stroker crank, we will be
checking clearances so we won't be using thread locker on the threads of our
rods yet. The rod bolts are coated with assembly lube and then torqued
sequentially to 15, 20, 30, and finally 38- foot-pounds.
Those specks are
specific to our aftermarket rods. Stock connecting rods will be tightened to
15, 20 and 24-foot-pounds. With the connecting rods tight we check that they
rotate freely on the crank and rotate them, to check the alignment and the
stamp numbers all face the same side.
Starting at the flywheel
side the rods are in order number three, number one, number four and number
two. Next, the front bearing is coated with assembly lube and slid onto the
crank. Again, make sure that the dowel pin hole is offset towards the flywheel.
That's followed by the oil slinger, which is disced, and set in place with the
dish pointing towards the crank pulley. The crank pulley keyway is tapped into
place. We check the fit of a stock crank pulley, making sure it fits over the
keyway.
Next, we mount the left
side of our freshly machined and cleaned engine case to our engine stand. We
install the four main bearing dowel pins and set the number two half-circle
crank bearing into the case and coat it with assembly lube. We also test fit
the rear number one bearing, which was cut down by our machine shop to match
our cut down thrust surface on the case, and mark the bearing so that lining it
up later will be easier.
Since we have a stroker
crank we need to check for crank and rod clearance to the engine case. We will
only be doing a test fit. If you're using a stock crank, this next process
isn't necessary.
The crank assembly is
pulled off the flywheel and the number one bearing is lubed and slid onto the
lubed crank at the rear. Making sure again that the dowel pin is offset towards
the flywheel. The crank is lightly set into the case while holding the number
one and number two connecting rods up. With the crank in place, the three full
circle bearings are rotated until they align with the dowel pins in the case. We
start with the number one bearing.
Then the front bearing
[is] aligned. With the bearings all lined up with the dowel pins, the crank
will settle fully into the case. Spin the crank over by hand to verify the
bearings are set in place. The bearings should not spin and an additional check
would be to set the remaining center half circle bearing onto the case at the
number two journal and check for a gap by trying to push the bearing towards
either side. If the bearing moves, there's a gap and the other bearings are not
lined up properly.
With the bearing
alignment confirmed, the bearings are marked at the side of the case so lining
them up again the next time will be easier. Back at our bench, the right side
case half is prepped by inserting the alignment dowel and the remaining center
half circle journal bearing is set in place on the case and coated with
assembly lube.
The right case half is
brought over to the stand and set in place onto the left case half while
keeping the number one and two rods upright to clear the case. The washers and
studs are set onto the main studs and snugged down lightly. Now we can rotate
the crank and check to see if the crankshaft or connecting rods hit the case. For
the most part the rods clear. But at the outside of the stroke, our rod bolts
hit the outside of the engine case. Interference is minimal and only at certain
angles but the bolt heads or the case must be clearanced to ensure the two will
not hit.
At this point, either
the case or the rod bolts can be clearanced. The rod bolts are the simplest to
clearance and won't require another thorough cleaning of the engine case. We
mark all eight of the rod bolt heads to indicate where the material will be
ground away. Note that the next torque sequence till most likely line up the
bolt heads up a few degrees clockwise past this point that the bolt heads sit
at now.
So that will be taken
into account when we grind the bolt heads down. The nuts and washers are
removed from the main studs and the right side case half is pulled off, set
aside and covered. The crank assembly is lifted from the left case half, set on
our flywheel and the left case half is covered. All the connecting rod bolt
assemblies are removed, the crank assembly is bagged, and then the bolt heads
are ground down at an angle so they won't fit inside the case.
We still leave a bit of
material for our 12 point socket. With all the bolts clearanced they are
cleaned re-coated with assembly lube at the heads and a drop of blue thread
locker is applied to the threads before the bolt is threaded back down in the
rod and tightened down in sequence again to 15, 20, 30, and 38-foot-pounds. Stock
rod nuts will be tightened to 15, 20, and 24 foot pounds and then either peened
over after being torqued, or of the rods do not have a notch for peening, thread
lock will be used on the nuts.
We test fit the crank
assembly into the engine case to make sure the clearanceing is sufficient and
with the rod clearance confirmed we pull the crank and bag it for safe keeping
until our next video. There we'll get back to the engine case that is sitting
on the stand and we'll install all the engine internals, drop the crank back
in, set the opposite case engine half in place, and get the short block torqued
down.
This will obliviously be
a multi-part series and while some of the steps are specific to our mild
performance build, these same processes will be used on a stock 1600cc build. If
you're looking for something to keep you busy until the next video is released head
over to JBugs.com for all your vintage Volkswagen parts and accessories.
Copyright © JBugs.
All rights reserved. All images protected by US and International copyright laws. No part of this website may be reproduced, distributed, or transmitted in any form or by any means.
All Prices subject to change without notice or obligation. Not responsible for typographical or photo errors. "Volkswagen", "VW","Beetle", "Super Beetle", "Bus", "Ghia", "Type 2", "Type 3", "Thing", "Rabbit", "Cabriolet", "Jetta", and "Golf" are trademarked by Volkswagen of America and are used for descriptive purposes only.