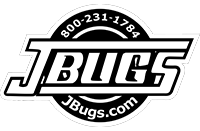
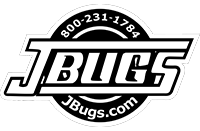
Your cart is currently empty.
Hello I'm Sam with
JBugs.com
We're in the midst of
out 1971 Super Beetle engine rebuild and in out last video we got the short
block bolted together. With the engine taking shape, we can set the crankshaft
end play and install a flywheel, but we'll start by modifying our new oil pump
to work with our full flow system. A full flow kit will allow us to run an oil
line out of the engine, from the pump to a filter then into an oil cooler if
we'd like and then back into our engine.
Our new oil pump is a
26mm unit made for late model dual relief cases using a flat cam. We need to
block off the stock exit port on the pump so that it will push oil out of the
pump cover that will be installed later. We tighten the pump in our bench vice,
with rubber pads on either side so that the pump isn't damaged. The exit port
is the upper left side of the oil pump as the pump would sit in the case at the
left of the oil pump drive gear hole. A 5/8" drill bit is used to open up
the port in the pump for a threaded plug and a 3/8" NPT tap is used to cut
the threads in the port on the oil pump.
With the threads cut
into the pump, we test fit the threaded plug and note that it sticks out just a
bit .We unthread it and grind down the high portion with a sanding disc. A burr
bit is used to clean up any rough surfaces inside the oil pump caused by
drilling and tapping. A scuff pad is used to clean up the outer diameter of the
pump where we drilled and cut the threads. Don't take too much material off the
pump, just remove any high surfaces.
The threads on the plug
are coated with red thread locker and it's threaded down into the oil pump and
tightened. The oil pump and gears are cleaned and we check that the gears spin
freely in the pump. Because we have a thicker than stock oil pump and an
aluminum cover, the four stock oil pump studs are removed from the case. We
thread a nut onto the stud, insert it through the pump cover and the oil pump and
mark how much thread on the stud is remaining. The stud is coated with blue
thread locker and threaded into the engine case up to the mark we made.
We measure how much
thread is sticking out of the case and thread the other three studs into the
same depth after applying blue thread locker. The inner oil pump gasket is
coated in GasGaCinch and slid onto the studs. It's followed by the oil pump. The
pump gears are installed making sure that the cam drive gear aligns with the
camshaft. The marks in the gears don't have to line up, just make sure they're
both visible.
The outer pump gasket is
coated with a thin film of Copper RTV and slid into place, followed by the oil
pump cover which is aligned with the outlet pointing to the left side of the
engine. Oil pump sealing nuts are threaded onto the studs and tightened down to
14-foot-pounds, along with the two engine case nuts above and the nut and bolt
below the oil pump again to 14-foot-pounds. The threads on a barb post fitting
are coated with blue thread locker and the fitting is threaded into the pump
cover and tightened down.
Now, at the back of the
engine, we set out new flywheel onto the crankshaft and tap it into place. A
new Chromoly gland nut is threaded into the crank to hold the flywheel in place
and tighten it down. Now, our first specialty tool is brought out. We have a
dial indicator with a magnetic base. They aren't too costly and they will be used
again later in our engine build. The magnetic base is used to attach the dial
indicator to the face of the flywheel when the flywheel is pulled or pried away
from the engine. The dial indicator is set by moving the arms and tightening the
set screws for the arms so that the end of the indicator is sitting against the
bell housing of the engine.
The fine adjustment
knob, on the indicator, is turned so that we can zero out the end needle. We
turn the gauge to zero out the dial. By pushing the flywheel back and forth we
can see that we have 0.044 of an inch of end play currently. When the end play
is set we want to have 0.003-0.005 of an inch. Aiming for the middle, we need
to add three shims that together ate 0.040 of an inch thick. The dial indicator
is pulled off of the flywheel, the gland nut is unbolted from the crank, and
the flywheel and dowel pin are marked so lining up the offset pin later will be
simple.
The flywheel is removed
and we install three new cleaned flywheel shims. Two 0.34mm and one 0.36mm which
will give us about 0.040 of an inch onto the crank. We reinstall the flywheel and
tighten the gland nut while using a flywheel lock to prevent the flywheel from
turning. The dial indicator is set in place and zeroed out again. We pull the
flywheel back and forth and we can see that we have 0.003 of an inch, which is
in spec. We can pull the flywheel off one last time and install a lubed O-ring
into the groove on the flywheel.
At the engine, a new
rear main flywheel seal is lubed on the inside diameter and pressed into the
engine by hand at first. We follow that up with a flywheel seal installation
tool which is tightened to push the seal all the way into the engine case. The
seal should be recessed slightly from the surface, not flush with the case. The
tool is un-threaded, the flywheel is set back into the crank again the gland
nut is threaded into the crank and a flywheel lock is threaded onto the engine
stud.
A torque wrench is used
to tighten the gland nut to 26-foot-pounds or 235-foot-pounds if the torque
tool isn't used. We like the torque tool as it doesn't require bracing the
engine and stand to tighten the gland nut. With the gland nut torqued we check
the end play one more time to verify the end play is in spec and we'll take a
break here until our next video. There we'll start the assembly of our top end
and install the head studs, test fit our pistons and cylinders, CC our head, and
set up the compression ratio for our engine.
Thanks for watching, in
the meantime check out some of our other how-to videos or head over to
JBugs.com for all your vintage Volkswagen parts and accessories.
Copyright © JBugs.
All rights reserved. All images protected by US and International copyright laws. No part of this website may be reproduced, distributed, or transmitted in any form or by any means.
All Prices subject to change without notice or obligation. Not responsible for typographical or photo errors. "Volkswagen", "VW","Beetle", "Super Beetle", "Bus", "Ghia", "Type 2", "Type 3", "Thing", "Rabbit", "Cabriolet", "Jetta", and "Golf" are trademarked by Volkswagen of America and are used for descriptive purposes only.