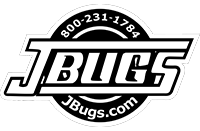
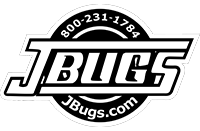
Your cart is currently empty.
Hello, I'm Sam with
JBugs.com. We're in the middle of mocking up out top end on our 1800cc engine
for our 1971 Super Beetle.
In our last video, we
just got done setting a cylinder head in place. We're mocking up the top end in
preparation for our 1.4:1 ratio rockers. Ratio rockers are an easy way to wake
up a VW engine and highly recommended if you have added dual carburetors and a
header to a stock motor. The stock cam is one of the limiting factors in
getting the fuel and air, into and out of the engine. 1.4:1 ratio rockers
increase the amount of lift from a stock camshaft from about 0.320 to about
0.420. That is the equivalent of installing a performance cam and the rockers
can be set up and installed in a few hours with the engine in the car.
The high lift rockers
require shorter than stock pushrods, rocker stand shims, valve lash caps, and
testing to ensure that the valve train works correctly. Adding to that, we also
have a stroker crank, which requires the same process.
At our engine, we first
test fit the new rocker assembly and see that it doesn't fit over the stock
studs. This is expected as the rockers include new rocker studs so the stock
studs are removed from the head, and the new studs are threaded in their place.
Next, we install hardened valve lash caps on top of the valve stems. The caps
are highly recommended whenever stainless steel valves are used to spread the
load between the rocker tips and the valve. High ratio rockers increase the
load substantially so consider the lash caps a must.
The rocker assembly is set back into place to confirm the fit and we can see the bosses aren't completely bottomed out on the stand. We pull the rockers off and install .0150 rocker stand shims on the studs so the rocker assembly can sit flat against the head. Now we can work on the rocker geometry and pushrod length. A push rod tool is lubed at both endsthe adjusted to the shortest length and placed into the cylinder head into the lifter bore into the case at cylinder number three in the intake valve. The engine is rotated over to top dead center for cylinder number three and we see the push rod drop. The push rod is moved over to the exhaust valve for photographic purposes and the rocker assembly is bolted down to the head.
Next, we back the valve
adjustment screws, which are located at the pushrod side on the new ratio
rockers, all the way out and then screw them in about half a turn and lock down
the nut. The push rod length is adjusted so it sits against the rocker adjuster
and tightened to zero lash at the valve as we'll be running Chromoly pushrods. Zero
lash is where we can spin the rod but there's no play in the rocker. If
[you're] using aluminum pushrods, set the valve play to 0.060 of an inch with a
feeler gauge.
The engine is turned
over by hand and stopped when the valve is pressed in as far as the rocker will
go. Our magnetic base from our dial indicator is removed, and the post is
threaded into the head at one of the intake manifold stud threads. The arms for
the indicator are moved and the indicator is positioned over the exhaust valve
seat, perpendicularly, and in line with the valve.
The indicator is pressed
in and set roughly at half an inch, pre-loading the indicator. Then locked in
place on the arm. We turn the engine over slowly again, noting the point where
the needle stops traveling in one direction and travels the opposite. This is
our max lift point and we zero our gauge at this point. The engine is turned
over slowly again and we count the gauge as it passes zero. It ends up turning
fully four times. It stops at 0.020, giving us a max lift of 0.420 inches.
Now we need to rotate
the engine over to the half lift point, half of 420 is 210. We rotate the
engine back to full lift and continue past zero twice then to the 0.010 marks. The
rocker geometry at this point, into the travel, is what we're adjusting. The
end result we want is for the rocker arm ends, at the valve and at the
adjuster, to be parallel with the head at the half lift moment. This will even
the loads on the valves and the adjuster to ensure a long life on the valve
train. Without current set up, the adjuster side is considerably lower than the
valve so the dial indicator is moved out of the way, the rocker assembly comes
off, and we swap out the 0.150 shims for a 0.300 shim.
The push rod is
lengthened to adjust to the valve and the dial indicator process is repeated and
the net result is that the adjusters come up a bit but is still much lower than
the valve. The whole process is repeated with a 0.600 shim and finally with a
0.600 and a 0.300 shim stacked together for a total of 0.900. Here, we get a
half lift point where the adjuster and valve are leveled. So the dial indicator
is moved to the side and the rocker assembly is pulled off.
The push rod is removed
and brought over to our workbench so we can mark and cut our new Chromoly
pushrods with a tubing cutter. The ends of the cut pushrods are cleaned up with
a burr bit. The push rods are blown out and cleaned thoroughly. A pair of old
lifters is used as a hammer and dolly of sorts to hold the push rod in place at
the bench while hammering the opposite end into place into the pushrod tube. The
push rods are blown out and cleaned again.
Back at the engine, two
push rods are lubed at either end and installed as the number three cylinder
which is set at top dead center. The valves are adjusted and the engine is
rotated over to confirm our geometry. With that, our mockup is complete. We can
now pull the head, cylinders, and pistons off the short block in preparation
for our top end assembly.
Our last two videos have been very tech heavy and whereas properly setting your engines compression ratio should be done for every engine build, setting up rocker geometry is a specific task required when building a stroker engine or installing high ratio rockers. Thanks for watching and keep an eye out for our next video where we'll complete our long block assembly. In the meantime, head over to JBugs.com for all your vintage Volkswagen parts and accessories.
Copyright © JBugs.
All rights reserved. All images protected by US and International copyright laws. No part of this website may be reproduced, distributed, or transmitted in any form or by any means.
All Prices subject to change without notice or obligation. Not responsible for typographical or photo errors. "Volkswagen", "VW","Beetle", "Super Beetle", "Bus", "Ghia", "Type 2", "Type 3", "Thing", "Rabbit", "Cabriolet", "Jetta", and "Golf" are trademarked by Volkswagen of America and are used for descriptive purposes only.