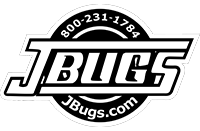
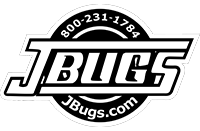
Your cart is currently empty.
Hi, I'm Sam with
JBugs.com With the discovery that our 1971 Super Beetle's engine needs to be
rebuilt, in our last video, we continue disassembling the short block. The
engine will be completely disassembled so that the case, crank, and other
components can be inspected. The case, if reusable, can be machined and reused.
We start by loosening
and removing all the smaller nuts and bolts around the perimeter of the case, then
follow with the six large case stud nuts. After making sure all the nuts,
bolts, and washers are removed, the case can be split apart. There are small
ledges at the front and back edge of the split in the case. Tapping the left
side of the case at the ledges while pulling at the head studs on the right
side case half, the case starts to open up. With more light tapping at the
lower engine stud, the right case half comes free.
Lifter clips are
inserted into the lifter bores on the right side case half to hold the lifters
in place. The right side case half is lifted up and off the engine and set
aside. Now, the crankshaft can be lifted up from the left case half by the one
and two connecting rods. [Lift] straight up and out of the case and set on our
bench. The camshaft is pulled straight up next and the cam plug is pulled from
the engine.
The six o-rings on the
main studs are carefully pried up, cut, and removed. The main and cam bearings
are removed from the case. A pair of needle nose pliers are used to remove the
four dowel pins from the main bearing journals. The pins should be tight in the
case and the holes should be squared in the journal. A wallowed out hole
indicates that the bearing is twisted and, most likely, the case should be
replaced.
The lifters are removed
from the case. Note that if you plan on reusing the lifters, place them into a
container and mark the positions so they go back in that same place into the
engine case. Now, the distributor drive pinion is pushed out of the case, and
the two pinion shims are removed.
The engine case is
flipped over and an impact driver and ground down chisel are used, to loosen
and remove the two oil release plugs. The oil pressure spring and pistons are
removed, noting the longer spring installs at the crank pulley side of the case
and, the shorter spring installs closest to the flywheel. The eight cylinder
head studs are un-threaded from the case by double nutting each stud, and using
a wrench or socket on the bottom nut.
I use a 17mm nut first
with a 15mm nut on top, which allows using a socket or a ratchet on the bottom
nut. The case is flipped over and the three oil sump plate studs are
un-threaded from the case. Note that the oil pick up stud has a nut inside the
case which must be unthreaded. The oil pick up stud is much longer than the
other two, as it runs up inside the case and holds the pickup in place. The
left case half disassembly is complete and the right side is very similar.
The lifter clips are
removed, and the lifters are removed from the engine case again noting their
position if they are going to be reused. The main and cam bearings are removed,
and a pair of needle nose pliers are used to remove the number two crank
journal dowel pin. The head studs and sump plate studs are removed. The right
side case half can be placed back on the left and loosely bolted in place for
safe keeping. At the bench, we can begin disassembling our crank. The rear main
bearing is slid off.
A hammer and punch are
used to remove the pulley woodruff key. The oil slinger is removed, followed by
the front journal bearing. Unless you have a set of snap ring pliers, stop here
and move to the connecting rods. Snap ring pliers are necessary to remove the
retaining ring, and caution is used sliding the ring over the crank so it does
not scratch the bearing journal. A press or puller are needed to remove the
distributor drive gear and the cam gear from the crank. Both fit so tightly
that they have to be heated up and slid onto the crank during installation.
We'll take our crank to
a shop, and have the gears pulled off so that we can pull off the number three
main bearing and inspect the crank. At the back of the crank, the four dowel
pins are removed. All should have a snug fit into the crank. Like the case, the
pins should fit tightly into the crank and the hole should be square in the end
of the crank shaft.
Wallowed out holes
indicate that the flywheel and crank had twisted either from a loose gland nut,
or too much horse power. If the holes are damaged, they may be able to be
drilled out for over-sized dowels. All four connecting rods are removed by
un-threading the rod nuts, and then lightly tapping the bolts to free the rod
from the cap. Keep each rod cap with the rod it came from as they are machined
an assembly. Note that the rod and the cap are stamped with matched numbers
that should line up.
Also note, the rod nuts
are one time use as they are peened over during installation. They are used to
keep the caps in place currently, but will not be reused. With that, our engine
disassembly is as compete as we can get it. The crankshaft will be taken into a
shop to have the gears pressed of, so we can reuse it. All of our case
hardware, head studs, dowel pins, and key ways will be cleaned and inspected.
The engine case will be
cleaned and taken to the machine shop for inspection. We had one theme in mind,
hoping that the engine was usable or at least re-buildable. But, that theme has
be modified slightly [but] still keeps to the spirit of the first. Those will
be shared in out next video though so stay tuned, thanks for watching, and
motor over to JBugs.com for all your vintage Volkswagen parts and accessories.
Copyright © JBugs.
All rights reserved. All images protected by US and International copyright laws. No part of this website may be reproduced, distributed, or transmitted in any form or by any means.
All Prices subject to change without notice or obligation. Not responsible for typographical or photo errors. "Volkswagen", "VW","Beetle", "Super Beetle", "Bus", "Ghia", "Type 2", "Type 3", "Thing", "Rabbit", "Cabriolet", "Jetta", and "Golf" are trademarked by Volkswagen of America and are used for descriptive purposes only.