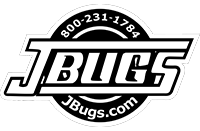
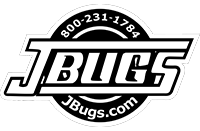
Your cart is currently empty.
Hi! Sam here with
JBugs.com.
We're almost done with
our 1800cc engine build. In our first few videos, we assembled a 74mm stroker
crank with I-beam connecting rods. We completed the short block and set up our
case for a full flow oil system. We also CC'd our cylinder heads, calculated
our compression ratio and set up the rocker geometry for our high lift rockers.
Now, we'll begin at our bench where all the pistons, cylinders, wrist pins, clips, and rings will be cleaned and prepped for assembly. The piston rings are re-installed on the pistons. Starting with the expander ring, this goes into the bottom groove with the painted marks lined up, not overlapped. The upper and lower oil rings are installed above and below the expander; followed by the lower compression ring, which has a notch at the lower outer edge.
Finally, the upper compression ring, which has a slanted upper inner edge. We lube the pistons and rings with lightweight oil and index the piston rings. Note the arrow on the piston points to the flywheel. We line up the oil rings at the top of the cylinder, the middle and the top compression rings at offset points, just above horizontal on the piston. A piston ring compressor is set around the piston and held in place tightly while a lubed cylinder is set in place above the piston and tapped down until the cylinder is just passed the bottom rings.
Again, note the cylinder
and piston that you're working on and make sure to align the cylinder properly with
the arrow on the piston pointing towards the flywheel. The piston and cylinder
are flipped over and the piston is pulled out of the cylinder just enough to
clear the wrist pin. Aviation sealant is brushed around the bottom sealing edge
of the cylinder, where it will meet the case. The lower 0.0040 steel cylinder
shim is covered with sealant as well and slid into place at the bottom edge of
the cylinder. Now a wrist pin clip is installed into the piston with a pair of
snap ring pliers at the inside edge of the piston that lines up at the flat
side of the cylinder. We push it back and forth to ensure that the clip is
properly seated into the groove. The number four cylinder is prepped in the
same manner, noting that the arrow on the piston points towards the flywheel.
At the engine stand, the number three piston and cylinder are positioned over the number three rod. A lubed wrist pin is slid through the piston, through the connecting rod, and into the piston at the opposite side. A clutch alignment tool is used to tap the wrist pin in completely. Another wrist pin clip is installed to keep the [rod] in place. A small screwdriver is used to make sure the clip is properly placed into the groove. The cylinder is pushed down over the piston and into the case, making sure that the cylinder shim does not fall out of place. The crankshaft is spun 180 degrees so the number four connecting rod is sticking out of the case and the number four piston and cylinder are installed in the same manner.
With both cylinders in
place in the engine case, we install the lower cylinder deflect tin, which
snaps in place in between the fins and the cylinders to the lower head studs. Don't
forget to install these pieces now as they are crucial to directing the air
through the cylinder fins and can't be installed once the heads and pushrod
tubes are in place.
The push rod tubes are
next to be prepped and we install new pushrod tube seals at each end of the
stainless steel windage style pushrod tubes. The windage style tubes have a
longer neck at the engine case which helps prevent oil from sloshing out of the
sump during hard cornering. Again we use aviation sealant and it's brushed onto
the pushrod tube seals. The tubes are placed into the engine case with the
longer edge inserted into the case and making sure to line up the welded seams
on the tube, at the top.
0.0040 copper head shims are set into place at the top of each cylinder. The cylinder head is set into place, onto the cylinder, while lining up the four pushrod tubes. The tubes are rotated a bit to ensure a good seal and to make sure the welded seam is still at the top of the tube. Assembly lube is dropped onto the cylinder head studs as well as all the head washers before they are set on all the head studs. Then all eight cylinder head nuts are threaded onto the studs lightly. A torque wrench is used to tighten the nuts down. The nuts are tightened down in two steps. The first step is to seven-foot-pounds in the pattern shown. The final step is to 23-foot-pounds, for our 10mm studs, on this engine. Or 18-foot-pounds if the studs are 8mm, in the pattern shown.
Our custom length
Chromoly pushrod ends are lubed and dropped into the pushrod tubes. The rocker
stand shims that we set up our engine with are set over the rocker arm studs. Followed
by the rocker assembly. Finally, the nuts which are just hand tightened. We're
just setting the assembly in place for now as we will pull the rockers off when
we first crank over the engine. A valve cover and bale are installed temporarily
to keep any debris out. The intake ports are stuffed with paper towels. Spark
plugs are threaded into the heads.
We tape off the oil
cooler passages and plug the engine case to keep anything from falling into the
engine. The whole process is completed on the opposite side of the engine at
the one and two cylinders. We run a section of oil hose from the oil pump to
the return on the case temporarily. A final touch is swapping out the stock
valve covers. Stock style valve covers will not work because the longer rocker
arms will end up hitting the cover. We'll install a set of stainless steel
valve covers from EMPI that are designed to work with the rockers. The new
covers are taller and have a square off shape to allow clearance for the longer
rocker arms. They also have a welded lip at the bottom edge to keep the gasket
in place and fit the cylinder head very snugly. The covers come with a new bale
as the stock bales are not long enough to fit over the new cover.
With that, our long
block is complete. Yes, we still need to properly install the rocker
assemblies, pushrods and set the valves; but we'll do that right before we
start the engine for the first time. In our next few videos, we'll cover
installing all the engine tin, all of the engine accessories and by the end;
we'll fire up the engine on our stand and cover the break-in and tuning
procedures. Thanks for sticking with us through this long series. In the
meantime, head over to JBugs.com for all your vintage Volkswagen parts and
accessories.
Copyright © JBugs.
All rights reserved. All images protected by US and International copyright laws. No part of this website may be reproduced, distributed, or transmitted in any form or by any means.
All Prices subject to change without notice or obligation. Not responsible for typographical or photo errors. "Volkswagen", "VW","Beetle", "Super Beetle", "Bus", "Ghia", "Type 2", "Type 3", "Thing", "Rabbit", "Cabriolet", "Jetta", and "Golf" are trademarked by Volkswagen of America and are used for descriptive purposes only.