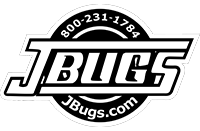
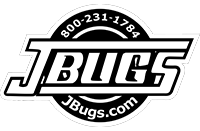
Your cart is currently empty.
Hi! Sam here with
JBugs.com
We're in the midst of
building a 1800cc engine for our 1971 Euro Look Super Beetle.
In our last video, we
assembled a crankshaft. It is set aside for the moment so we can view the
engine case and get ready to drop the crank and the other engine internals into
the case. By the end of this video, we'll have the short block assembled and
torqued together.
We have our freshly
machined engine case back from the machine shop. It's been machined half a
millimeter, or twenty thousandths over, on the line bore and the thrust area
has been machined down to fix the previous ware. The machine shop cut down the
number one bearing, after the case was cut, to match the new thrust size of the
case. If your case needs machine work done to the thrust surface, make sure
that your machine shop cuts an appropriate sized bearing down for you.
Our engine case had been
cleaned thoroughly and so we don't have to mention it every step; every part we
install is cleaned with parts cleaner before its fit or test fit to the case. We
start with the case already mounted to our engine stand, as it was in our last
video, and we'll begin by installing our new distributor drive gear shims. Two
shims are coated with assembly lube and set inside the case on the drive gear
shelf. The pinion drive gear spring is pressed into place on the gear; the gear
is coated in assembly lube, and slid into the engine case through the shims and
into the lower shelf inside the lower case.
For the next step
ideally, you'll want to use the distributor that will be used in the engine
later. In our case, a new SVDA distributor from PerTronix with an Ignitor 3
module is prepped with a distributor clamp. The distributor, with the cap
removed, is slid into the case and drive gear by rotating the distributor shaft
until it lines up with the gear. What we're doing here is lining up the timing
for top dead center for the number one cylinder. At this point, wherever you
point the rotor will be the number one top dead center. We make note of this as
originally VW distributors typically line up in the opposite directions of
aftermarket distributors.
Once we have the rotor
pointing to where we would like the number one top dead center to be, we attach
the clamp to the case and install the rotor and distributor cap. Next, we
install new oil sup plate studs. Note that the oil pickup stud is longer than
the other studs as it has a nut inside that holds the pickup tube in place. I
actually like to use the longer studs at all six holes along with a nyloc nut
inside the case to hold the studs in place.
I also put a little blue
thread locker to ensure the studs will not un-thread when changing the oil
years down the road. With the three studs and nuts installed on each case half,
we can drop our crankshaft assembly in place into the left case half. We've
already installed all four dowel pins and the number two bearing in the left
case half and the bearing is lubed. The crank is lightly set into the case
while holding the number one and two connecting rods.
With the crank in place,
the three full circle bearings are rotated until they align with the dowel pins
in the case. We start with the number one bearing, then the front bearings are
aligned. With all the bearings lined up with the dowel pins, the crank will
settle fully in the case. We spin the crank over by hand to verify the bearings
are set in place. The bearings should not spin. An additional check would be to
set the remaining center half circle bearing onto the crank and check for a gap
by trying to push the bearing towards either side. If the bearing moves,
there's a gap and the other bearings are not lined up.
New lifters are covered
with assembly lube and we run a small bead around each lifter bore before
dropping four lifters into the case. Three new cam bearings are set into the
case noting that the cam thrust bearing, the only bearing that has lips on
either side, sits in the saddle closest to the oil pump bore of the case.
We can prep for the cam
by spinning the crank over until the timing marks on the drive gear are just
above the split in the case. The cam is set into place in the case and the
timing mark on the cam is lined up between the two marks on the drive gear. With
the cam in place, rotate the crank back and forth to check the thrust on the
cam gear. If the cam were to pop out of the case, you'd want a different
camshaft as if the thrust cut or the angle of the cut on the gear, is
incorrect.
Our cam spins over
smoothly and does not pop out of the case so we will continue. A new camshaft
plug is coated with GasGaCinch around the perimeter and set into place into the
cam groove in the case. The six main stud O-rings are slid onto the studs down
to the case groove and coated with a bit of assembly lube. We're almost ready to
set the right side case half in place. So we get it prepped at the bench by
installing the three remaining cam bearings into the saddles and coat them with
assembly lube.
Just like we did on the
left side the lifters are covered with assembly lube, as are the lifter bores and
the lifters are dropped into the case. The lifter clips are installed from the
outside of the case to hold the lifters in place when we lift the case over. We
apply GasGaCinch around the outside perimeter of the case and wipe up any
excess sealant.
The sealant only needs
to be on the outer flat surfaces of the case and into the cam plug saddle at
the rear.
Now, it's time to put
the two case halves together for good. The number one and two connecting rods
are pointed straight up and the right side case half is dropped onto the left
side and tapped down gently. The six main, and the two camshaft case washers
are coated with aviation sealant and set in place onto the studs which are
coated with the sealant as well. The case nuts are threaded on by hand then a
torque wrench is used to tighten the two 13mm nuts at the cam studs to
14-foot-pounds. The six main studs are tightened in the displayed pattern. Starting
at the two center studs then crisscrossing each of the outer four studs. In a
step tightening sequence of 15, 20, and finally 24-foot-pounds.
Rotate the crank in
between each step to make sure the crank does not lock up. If the crank does
not spin, stop. Pull the right side case half off and check the alignment of
the bearings and dowel pins.
All of the outside
perimeter case bolts, studs, and washers are coated with aviation sealant just
like we did with the mains. All the outside hardware, with the exception of the
two nuts above and the bolt below the oil pump, are tightened to
14-foot-pounds. The nuts and bolts above and below the oil pump will be
tightened after the oil pump is installed.
Next, we flip the case
upside down and remove the lifter clips. We'll install the pressure relief
valves. We start at the rear valve and squirt some assembly lube into the port
before lubing the valve and the short spring and dropping them in, the valve
going first with the open end towards the bottom of the engine. We follow that
by installing a new crush ring on the relief port screw and then threading that
in place firmly. We're going to run an oil temperature gauge so we swap out the
stock screw for a VDO temperature sending unit.
At the front bleed port,
we'd normally install a valve, followed by the long spring and cap it with a
gasket and screw. However, we're going to install a bolt on full flow kit which
installs at the front port and does not use the valve or spring. The kit
consists of a threaded sleeve bolt which installs through a banjo fitting and
sealing washers install at either side of the fitting before the assembly is
threaded into the engine case. The bolt head is tightened down while keeping
the banjo fitting pointed towards the left side of the engine case.
We'll finish up the
bottom side of the engine by installing the oil screen and sump plate. I like
to use an oil suction kit which has an aluminum sump plate and a billet
aluminum pick up extension. The pick-up has a removable mesh screen that is
held in place with a spiral lock spring. The pick-up slides in first and has
internal O-rings for a very tight fit.
A single sump plate
gasket is coated with GasGaCinch and pushed into place onto the studs. The sump
plate is set onto the engine, followed by sealing washers and nuts.
The six sump plate nuts
are tightened down to five-foot-pounds and we'll take a break here until our
next video where we'll drill, tap and install our g pump for the full flow
system, set the crankshaft end play, and install the flywheel. Until then,
check out some of our other how-to videos or stop by JBugs.com for all your
vintage Volkswagen parts and accessories.
Copyright © JBugs.
All rights reserved. All images protected by US and International copyright laws. No part of this website may be reproduced, distributed, or transmitted in any form or by any means.
All Prices subject to change without notice or obligation. Not responsible for typographical or photo errors. "Volkswagen", "VW","Beetle", "Super Beetle", "Bus", "Ghia", "Type 2", "Type 3", "Thing", "Rabbit", "Cabriolet", "Jetta", and "Golf" are trademarked by Volkswagen of America and are used for descriptive purposes only.