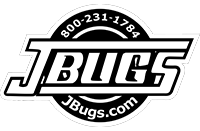
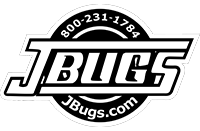
Your cart is currently empty.
Hi! Sam with JBugs.com. In
our last video, we started bolting on all the components that will complete our
1800cc stroker engine. We took a break after getting the intake manifold set in
place and today we'll pick up where we left off. We'll get the rest of the serpentine
belt components bolted on, install flanged heater boxes, two tip gt exhaust system, and all the remaining
parts we'll need to make a turnkey engine.
We start by installing a
pulley spacer on the crankshaft which will offset the pulley so it lines up
with the serpentine belt tensioner. The new crank pulley is then tapped into
place followed by a crank pulley bolt and washer. The bolt is tightened with a
30mm socket or large crescent wrench.
At the alternator, a
spacer is slid over the shaft before installing the pulley keyway. The new
alternator pulley is installed next followed by a lock washer and nut. The
tensioner pulley bolt is unthreaded from the adjuster bracket so we can pull
off the pulley and install the serpentine belt. Then the pulley and bolt are
threaded back into the bracket.
The tensioner pulley
bolt has a decorative cap that is held in place with an Allen set screw. With
it removed, the bolt can be tightened to the bracket and the cap can be set
back in place. The bracket is adjusted by loosening the two Allen screws and
sliding the pulley and bracket towards the belt to tighten. With the belt
tightened, the two bracket bolts are tightened and next well install the spark
plug wires.
We start with the longer
1-2 wires which are routed behind the intake manifold. This required removing
the dust seals and the center wire plug holder on the shroud as it is a very
tight fit. The boots a re-installed and the wires are plugged into the
distributor cap. The 3-4 wires are shorter and much easier to rout and install.
The wires are pressed into the spark plug wire holders on the fan shroud once
they are routed into place. We don't fully install the wires at the plugs as
the plugs will be coming out before we start the engine.
At our workbench, we'll
prep our new PerTronix low resistance coil which is needed for our PerTronix
igniter 3 SVDA distributor. We install push on electrical terminals at both the
threaded studs. On the positive terminal, we'll install a triple push-on connector as we need a terminal for the
positive ignition wire, the coil wire, and the electronic ignition. On the
negative terminal, we install a double connector for the electronic ignition
and a tack lead.
At the engine, the coil
is bolted to the fan shroud and the coil wire is connected. Now the engine is
rotated so the 1-2 cylinder head is up so we can thread on the thermostat. It
is threaded all the way in then backed off so the flat edges are perpendicular
to the engine case. The thermostat bracket is set in place, over the thermostat
aligning the bracket with the flat edges on the thermostat, and then the engine
case mounting stud. A bolt and large diameter washer are used to attach the
thermostat to the bracket.
At the case, a nut and
washer are threaded on and the bracket is slid up on the case to close the
flaps and the nut is tightened. The flat heater channel tin is screwed to the
curved heater channel tin at the hole closest to the case and to the engine
case. Our case was stripped out here so we tapped it to an 8/125mm and used an
appropriate sized Allen bolt. Now all the exhaust studs are threaded into the
cylinder heads and new exhaust gaskets are installed at the back exhaust ports.
Now, we'll weld some
flanges on to our two tip exhaust system to match our 1 1/2 inch flanged
performance heater boxes. A heater box is bolted to a used cylinder head. Then
the exhaust is bolted to the opposite side lower stud and rotated so it sits next to the flange of the heater box. The
exhaust pipe is cut with a Sawzall in line with the heater box flange. The
exhaust is removed from the head, the pipe is sanded down to remove the paint, a
weld on flange is slid over the pipe, and
the exhaust is bolted back to the head at both studs. The new flange is bolted
to the heater box and the flange is welded to the exhaust pipe. The same
process is repeated on the opposite side pipe using the opposite heater box and
flipping the cylinder head around.
The heater boxes are slid onto the exhaust ports and low profile 12 point nuts are threaded down loosely to hold the heater box in place. The nuts are not going to be tightened down yet. New exhaust gaskets are installed at the front exhaust ports, the modified exhaust is set in place over the studs, and low profile nuts are loosely threaded down to hold it in place. Because we have a stroker engine, the heads sit a little farther apart than stock so the exhaust pipe at one opposite head needs to be pulled slightly to line up both of the studs. Now, exhaust gaskets are slid in between the heater box and the exhaust flanges. The bolts for the flanges are installed along with low profile nuts. With both heater box to exhaust pipe connections tight, the nuts at the head for the heater boxes are tightened down and the long tabs from the heater boxes are screwed into the heater channels.
At the back of the fan
shroud, the thermostat bar is installed to connect the left and right flaps and
the return spring is installed from the fan shroud to the crossbar. Now is a
good time to make sure that you've installed the screw from the fan shroud to
the hoover bit if your engine still has the hoover bit. The lower doghouse exit
duct is installed at the back of the fan shroud, followed by the upper duct. The
doghouse front engine tin has a cutout for the exit duct and bolts to the left
and right cylinder shrouds but can't be bolted in place currently as our engine
is bolted to our engine stand.
At the front of the
engine, after making sure the heat riser ports on our exhausts are drilled out,
we install the left and right intake manifold pre-heat tubes. [They] slide into
small holes under the intake manifold at the left and right sides. The tubes
line up with the heat riser flanges at the number two and four exhaust ports and
are essential to keep the intake manifold from icing up.
Gaskets are set in
between the flange and the tube and nuts and bolts are installed and tightened
down to secure the connection. At the carburetor, we unthread the fuel inlet
line and swap it out with the plug at the front of the carburetor. This will
allow the fuel line to come around the front of the carburetor as there is not
much clearance behind the [carburetor] and the intake manifold.
Now, we can set the rear
engine tin in place. and we can show how the intake preheat pipe would install.
Through the tin, lining it up with the notch in the cylinder deflect tin and it
would attach to the lower exhaust stud if we were using it. We won't be though,
so we need to block the hole in the engine tin. Cardboard and a marker are used
to make a template. The template is used as a guide and we cut a piece of sheet
metal that we bolted in place to the tin and blocked the hole.
With the rear engine tin
pulled, the screw for the deflect tin that is closest to the exhaust port is
tightened after making sure that the opposite end nut insert lines up with the cylinder shroud and breastplate. The rear
engine tin is set in place on the engine again and loosely set in place to the
breastplate and to the left and right cylinder shrouds. Next, we install the
preheat pipe tins at the left and right cylinder shrouds. With all the screws
lined up and threaded in place, their all tightened.
Since we will be breaking in our engine on the stand, we'll install an oil filter bracket by using a long bolt at the outer engine tin screw at the left of the engine. We aren't using a stock muffler but we are using heater boxes so aluminum fresh air fan shroud hoses are routed down through the rear engine tin, hooked up to the heater boxes, and shaped around the exhaust tubes. Fresh air hose seals are then slid over the hoses and pushed down to the rear engine tin and the hose is slid in place over the fan shroud.
At the right of the engine,
the air hose has to be clearanced for the oil filer breather hose. The oil
filler breather hose is attached to the port at the bottom of the air cleaner
we installed earlier and pushed into place onto the oil filler. Next, we
install the fuel line and since we want to check the fuel pressure as we're
installing a new fuel pump we have a test line set up with an inline pressure
gauge. The EGAS carburetor has a much larger than stock 5/16 inch inlet. We use
7mm hose at the carburetor, we use the cut off end
of an old plastic fuel filter [to step] down the fuel line to 5mm, and that
hose is routed to the bottom outlet port.
Since we'll be running
our engine on a bench, we don't have a front engine tin in place to run the
stock metal fuel line through, so we use a long length of 5mm fuel hose and
attach it to the top inlet port at the fuel pump. A length of 3.5mm vacuum hose
is pressed in place on the vacuum port on the carburetor, trimmed to length, and
attached to the vacuum diaphragm on the distributor. For safeties sake, we zip
tie the fuel hose from the pump to the carburetor to the distributor clip to
prevent the line from dragging on the alternator pulley.
Now we prep the oil
filter adapter and apply blue thread locker to the filter threaded boss and the
hose barbs. [We] thread them into the adapter and tighten the hose barbs with a
wrench. Assembly lube is applied to the sealing ring on the oil filter and the
oil filter is threaded onto the adapter. Do not over tighten the filter, once
the filter contacts the seal, turn a half turn and it's tight. The length of
oil hose we've attached to the oil pump and return is pulled off from the
return routed up to the inlet and oil cooler adapter and trimmed to length. Hose
clamps are slid onto the hose before it is attached to the filter adapter and
the clamps are both tightened. The remaining section of hose is used to attach
the outlet of the filter to the return on the engine case after trimming it to
length and hose clamps are used to secure the hose at both ends. The threaded
hose fitting is tightened to the return of the adapter.
We install the rear
engine tin block off plate with a trimmed
and bent off piece off sheet metal that
we fabricated from the template we made earlier. The teardrop shaped piece of
metal has a long tab that we cut and bent to slide under the large hole in the
tin. The smaller hole secures the other end with a tin screw that attaches at
the breastplate.
Finally, the wires for
the electronic ignition are routed to the coil, trimmed to length, stripped, and
quarter inch terminal ends are crimped onto the ends. The red wire is plugged
onto the positive terminal on the coil. The black wire is plugged onto the
negative terminal. It is important to note that the original Volkswagen wire,
from the main harness at the coil, is black and goes to the opposite, positive
side of the coil. We've only removed the coil to emphasize the position of the
wire.
With that, we're just
about ready to fire [up] our engine for its break-in run. We'll cover that
process in our next video where we'll fill the engine with oil, pull the
pushrods and plugs, crank the engine over to build oil pressure before we
install the pushrods and rockers, the plugs and fire the engine up for the
first time. In the meantime, check out some of our other tech and how-to videos
and when it's time to order parts for your vintage Volkswagen, head over to
JBugs.com
Copyright © JBugs.
All rights reserved. All images protected by US and International copyright laws. No part of this website may be reproduced, distributed, or transmitted in any form or by any means.
All Prices subject to change without notice or obligation. Not responsible for typographical or photo errors. "Volkswagen", "VW","Beetle", "Super Beetle", "Bus", "Ghia", "Type 2", "Type 3", "Thing", "Rabbit", "Cabriolet", "Jetta", and "Golf" are trademarked by Volkswagen of America and are used for descriptive purposes only.