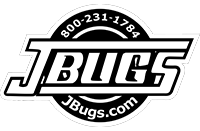
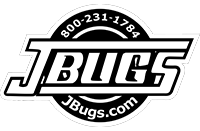
Your cart is currently empty.
Hello! Sam here with JBugs.com With
the long block for our 1971 Euro Look Super Beetle complete, we can now install
all of the parts needed to make it into a turnkey engine. We've got all of the
original engine tin cleaned up and we
have a number of new components that we'll be installing. Such as a 38 EGAS carburetor kit and a serpentine
fan belt system. All that starts with some quick prep to our new cylinder head so
that we can install the original thermostat, and pushrods, through the head as
Volkswagen designed.
Looking down from the top of our
cylinder head we can see that there is some light between the cylinders but not
quite enough room for a thermostat rod. We use a drill and a 3/16" bit to
open up the head for the push rod. With the head drilled out a bit, we can test
fit our fan shroud. Guiding the rod through the head and we make sure the
thermostat can be connected to the rod
at the engine case at the bottom of
the head.
With the fit confirmed, we flip our
engine over and [install] the small head deflect tin that we pulled from our original heads. The tin has four legs
that get pressed in between the fins in the cylinder head. With the engine
upright again, we assemble a new doghouse oil cooler adapter. The shorter of
the three studs threads into the adapter at the bottom and the other two longer
studs install at the top of the adapter. A new oil cooler is flushed out, along
with the adapter, and new seals are installed between the cooler and the
adapter.
Complete engine gasket kits come
with three different oil cooler seals. The dog house oil cooler and adapter use
four of the thinner, larger diameter seals. Two seals install between the
cooler and the adapter before new washers and nyloc nuts are installed. The
nuts are tightened to five-foot-pounds and make sure to install the hoover bit
engine tin into the upper two studs if you have it.
Two more oil cooler seals install at
the engine case before the oil cooler and adapter are set in place. Washers are
installed under the three studs, followed by new nylocs. The nuts are tightened down to 14-foot-pounds. We're going to swap out the original style distributor
clamp for an aluminum clamp. We set the engine to top dead center at the number
one cylinder. The distributor and clamp are removed from the engine. The
original style clamp is removed from the distributor.
We install a new mounting post for a
billet aluminum distributor clamp which is tightened to 14-foot-pounds. The new clamp is set over the new
post. Our distributor is slid in place and we turn the rotor to make sure we
can push the distributor all the way into the engine. The distributor is lined
up to our number one mark. The cap is reinstalled and a new nut is installed at
the new post and tightened to 14-foot-pounds.
At each head, blue thread locker is applied to the intake manifold studs before
they are threaded into the cylinder heads.
Next, the dual port cylinder shrouds
are set in place at the appropriate head and tin screws are installed at each
head to hold the tin in place. At the 3-4 cylinder head, the long single piece heater channel tin is screwed in place at
the cylinder tin at the flywheel side of the cylinder, and to the engine case
at the bottom of the engine.
We follow with the shorter, two-piece heater channel tin at the 1-2
cylinder head. The curved tin is screwed in place at the cylinder tin at the
flywheel side of the cylinder and to the engine case across the bottom. Make
sure the tin is clear of the exhaust ports, before tightening all the screws. At
the pulley side of the engine, the breastplate
is set into place and screwed into the engine case.
Next, we'll install the lower air
deflector tins which bolt to the pulley side of the engine. The tin at the 1-2
cylinder head has a notch for the original warm air
or pre-heater stovepipe, which would
connect to the tin and the lower exhaust stud. We won't be using the stove pipe
so this tin at this side is screwed in place but we leave the screws loose as
other pieces of tin will attach here later.
Now, we'll set the fan shroud in
place so we can get our new carburetor and intake manifold mocked up. Spark
plug wire holders are pressed into the holes on the fan shroud. With the major
engine components in place, we'll start prepping our new 38 EGAS carburetor and
intake manifold for mock-up. The EGAS
carburetor is a derivative of the progressive style carburetors. It has two,
38mm barrels that open up at the same time for more power and performance. Another
added benefit over the progressive carb is that the EGAS carburetor position on
the manifold with the choke element and wire, away from the fan shroud.
There is no need to worry about
shortening out on the fan shroud. We first verify the baseline setting on the idle mixture screws, at one and a half
turns out. The idle screw is set at one turn, in once it touches the
accelerator lever, with the choke butterflies open. Next, blue thread locker is
applied to the four intake manifold studs and they are threaded into the intake
manifold. A base gasket is set in place on the manifold and followed by the
carburetor. At the rear left stud, the [carburetor] return spring bracket is
set in place and spring washers are set over the studs followed by nuts which
are threaded down and tightened.
The carburetor return spring is
attached to the bracket and hooked up to the linkage. We initially hooked up
the spring to the upper hole but later we'll swap it to the lower hole. The
carburetor linkage stud is coated with blue thread locker and threaded into the
intake manifold. Followed by a washer, the linkage lever, another washer, and a
nyloc nut. The nut is tightened to the
point where the lever still pivots but does not wobble. The throttle linkage
bar is assembled and attached to the lever on the intake manifold and the
carburetor. We swap the position of the spring on the linkage in a moment. We
adjust the choke, first loosening the three screws on the element then opening
the throttle to allow the choke to open. We twist the choke element to close
the flaps at the top of the carburetor. Once the flaps touch, we stop twisting
the choke and tighten the screws.
An air cleaner base gasket is set in
place at the top of the carburetor. Followed by the air cleaner base plate. Note
that we've installed the plastic vent fitting into the base and pointed it
towards the number one cylinder. The air cleaner element is set in place onto
the base plate and followed by the air cleaner cap and wing nut. New paper
intake manifold gaskets are marked to trim and fit with the original cylinder
shrouds. Their set in place at the heads at either side and the left and right
end castings are set in place at each head.
Now the carburetor and intake manifold are set in place between and into the two end castings. The intake manifold brace is set in place over the fuel pump stud and bolted onto the side of the intake manifold. This will keep the [carburetor] and intake manifold secure while we adjust the carburetor linkage. Note that the brace is not intended to be used with a stock style fuel pump but we will be modifying it so that we can. We test the carburetor linkage operation and see it hits the fan shroud before allowing full throttle. As we mentioned earlier, we flip the [carburetor] return spring and the linkage arm positions on the carburetor bell crank.
The linkage arm is readjusted to
allow the linkage to open the carburetor completely and not hit the fan shroud
at full throttle. The carburetor, manifold, and end castings are removed and a
lower fuel pump gasket is coated with copper RTV and set in place over the fuel
pump studs.
The fuel pump flange is dropped in
place and followed by four upper gaskets. The four gaskets are used to lower
the fuel pressure, spacing the fuel pump further away from the fuel pump
flange. A short, alternator style fuel pump drive rod is lubed and inserted
into the flange, pointed end first. The new alternator style fuel pump is
installed.
Now we can mock up and modify the
intake manifold brace. We lucked out and the taller mounting stud from our
billet distributor clamp happens to be in the
perfect position if the bracket is flipped. We remove the nut that holds
the distributor clamp in place and set the bracket onto the stud. We can see
that the brace will have to be clearanced
for the fuel pump inlet and outlets. We mark it and grind it down. With the
bracket ground down to clear the fuel pump the carburetor, intake manifold and
end castings are all test fit.
An oil T fitting is threaded into the engine case along with the manual pressure gauge and a two-pronged oil pressure switch that will send a signal to a warning light and a pressure gauge later. The manual pressure gauge we install now will allow us to confirm we have oil pressure before starting our engine for our first time. The heat riser tubes, exhaust, and rear engine tin are all set in place to temporarily test the fit. The dip stick is installed. An oil filler breather collar is slid over the original oil filler tube on our original oil filler. We follow that with the road draft tube. We confirm that there is a small slit at the bottom of the tube and the filler is set in place into the engine tin.
To make installing our new
serpentine belt system easier, the heat risers, rear engine tin, and fan shroud
are set aside. The two front alternator stand studs are removed and replaced
with longer studs. An oil deflect plate is set in place over the studs noting
the correct orientation of the plate. The alternator stand is set in place. To
make a bit of room, the carburetor and intake manifold is removed. The fuel pump is temporarily loosened so the serpentine
belt tensioner can be set in place. The nuts for the fuel pump and the stand
are tightened to 14-foot-pounds. The oil
filler is moved in place with a new gasket. The oil filler nut is threaded
through the filler and into the stand and tightened.
At our workbench, a new 90amp alternator is prepped by installing the
original three-piece backing plate. After
making sure that the keyway is in place, the fan hub is slid onto the
alternator. Followed by the fan, washer, and the fan nut. The alternator and
fan are set into the fan shroud and screwed into place.
Back at the engine, the fan shroud
and alternator are set into place while carefully guiding the thermostat rod
through the 1-2 cylinder head. We reset the shroud to make sure it sits between
the left and right cylinder shroud. The 3-4 end casting is pulled off the
cylinder head. The carburetor and intake manifold, with boots and clamps, slid on, is set into place onto the
alternator and set into the 1-2 end casting. The 3-4 end casting is set in
place and four, 12 point slim line intake manifold nuts, are threaded in place
and tightened to 14-foot-pounds. The slimline nuts accept a 10mm 12-point socket or
wrench and are perfect for places with tight access like the intake manifold or
exhaust.
The intake manifold boots are slid in place on the end castings and
all four clamps are tightened. A T bolt style alternator clamp is placed around
the stand and alternator and tightened down. The intake manifold brace is
attached to the distributor clamp post and with that,
we'll take a break.
We'll be back soon, we'll install
the rest of the serpentine belt system, the rest of the engine tin, our exhaust
system, and all the other components that are needed to get our engine fired up
on the engine stand. Stay tuned and in the meantime
head over to Jbugs.com for all the vintage Volkswagen parts you'll need for
your vintage Volkswagen.
Copyright © JBugs.
All rights reserved. All images protected by US and International copyright laws. No part of this website may be reproduced, distributed, or transmitted in any form or by any means.
All Prices subject to change without notice or obligation. Not responsible for typographical or photo errors. "Volkswagen", "VW","Beetle", "Super Beetle", "Bus", "Ghia", "Type 2", "Type 3", "Thing", "Rabbit", "Cabriolet", "Jetta", and "Golf" are trademarked by Volkswagen of America and are used for descriptive purposes only.